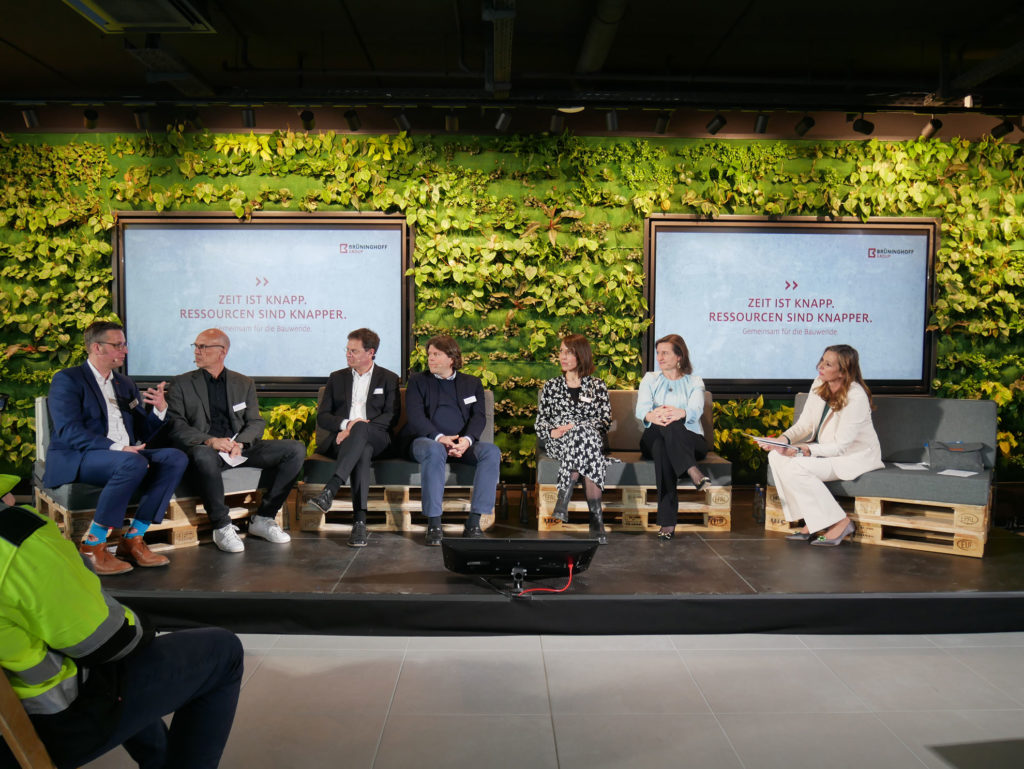
Wenn der Klimaforscher im Betonfertigteilwerk...
Expertenrunde zum Thema „Die Bauindustrie im Klimawandel – warum zirkuläres Bauen alternativlos ist“.
Klimawandel und zunehmende Ressourcenknappheit – Themen, welche die Baubranche kontinuierlich beschäftigen und beeinflussen. Auch die Brüninghoff Group arbeitet schon lange mit der Grundeinstellung, nachhaltig und umweltfreundlich zu bauen. So war das Motto „Zeit ist knapp. Ressourcen sind knapper. Gemeinsam für die Bauwende.“ sowohl beim Bau als auch bei der Eröffnungsfeier des neuen Betonfertigteilwerks von Brüninghoff wegweisend. Ende März wurde dieses mit einer exklusiven Feier am Standort in Heiden eröffnet. Das Highlight: Eine Diskussionsrunde zum Thema „Die Bauindustrie im Klimawandel – warum zirkuläres Bauen alternativlos ist“. Dazu waren namhafte Experten auf den Gebieten Klimaforschung, Kreislaufwirtschaft und Nachhaltigkeit geladen. Neben den Gästen vor Ort waren zahlreiche Zuschauer per Livestream zugeschaltet.
Unlängst wurde die Eröffnung des neuen Betonfertigteilwerks am Hauptsitz der Brüninghoff Group in Heiden gefeiert. Schon während der Planungs- und Bauphase setzte das Unternehmen auf Klimafreundlichkeit und Nachhaltigkeit. Für optimierten Ressourceneinsatz im Betrieb und bei der Produktion wurde der Neubau unter anderem mit einer Photovoltaikanlage, einer Regenwasserzisterne sowie mit elektrischen Ladesäulen ausgestattet.
Vor der offiziellen Feier fand eine interne Eröffnung des Werks mit den Mitarbeitern der Unternehmensgruppe statt. Um elf Uhr wurden schließlich rund 60 externe Gäste vor Ort und circa 500 Zuschauer im Livestream von Brüninghoff-Geschäftsführer Frank Steffens begrüßt. Themen der 30-minütigen Rede waren das Bauprojekt selbst, die zugrunde liegende Intention sowie Besonderheiten, Kreislaufgedanke und Nachhaltigkeitskonzept. Überdies wurde den beteiligten Mitarbeitern Dank ausgesprochen.
Zukunftsweisende Diskussion zum innovativen Denken
Nach der Begrüßungsrede begann die Hauptattraktion der Feier: eine exklusive Diskussionsrunde zum Thema „Die Bauindustrie im Klimawandel – warum zirkuläres Bauen alternativlos ist“. Neben Frank Steffens befanden sich Sabine Oberhuber, Nachhaltigkeitsexpertin und Pionierin der Kreislaufwirtschaft, der Polar- und Klimaforscher Markus Rex, Christian Berg, Universitätsprofessor und Experte für Nachhaltigkeit in der Wirtschaft, die Zukunfts- und Trendforscherin Christiane Varga, sowie Thomas Bader, Geschäftsführer der Leipfinger-Bader Firmengruppe, unter den Diskutanten. Moderiert wurde die Runde von der Wissenschaftsjournalistin Kristina zur Mühlen. Auf der Agenda standen Themen wie Kreislaufwirtschaft, Nachhaltigkeit im Bau sowie die Entwicklung der Gesellschaft. Hierbei waren sich die Experten einig, dass Materialwirtschaft, fortschrittliches Denken und systemische Regulierung die Hauptstellschrauben für die Umsetzung von nachhaltigem Bauen darstellen. So sind Innovation und Investition zwei zentrale Faktoren. Zudem muss die Bauwirtschaft mit ihren kreislauforientierten Lösungen stärker in die öffentliche Wahrnehmung rücken und mehr Gehör finden. Überdies gilt es, die Attraktivität von nachhaltigem Bauen zu steigern – beispielsweise mithilfe einer höheren finanziellen Förderung. Denn das Interesse an umweltfreundlichen Materialien und Gebäuden ist bereits vorhanden.
Die rege Diskussion zeigte, dass das Thema Nachhaltigkeit im Bau schwierige Fragen mit sich bringt, auf die es keine einfachen Antworten gibt. Umso wichtiger ist es, dass die Innovatoren und Visionäre der Gesellschaft mit gutem Beispiel vorangehen. Abgeschlossen wurde die Eröffnungsfeier des Betonfertigteilwerks mit einer Werksführung.